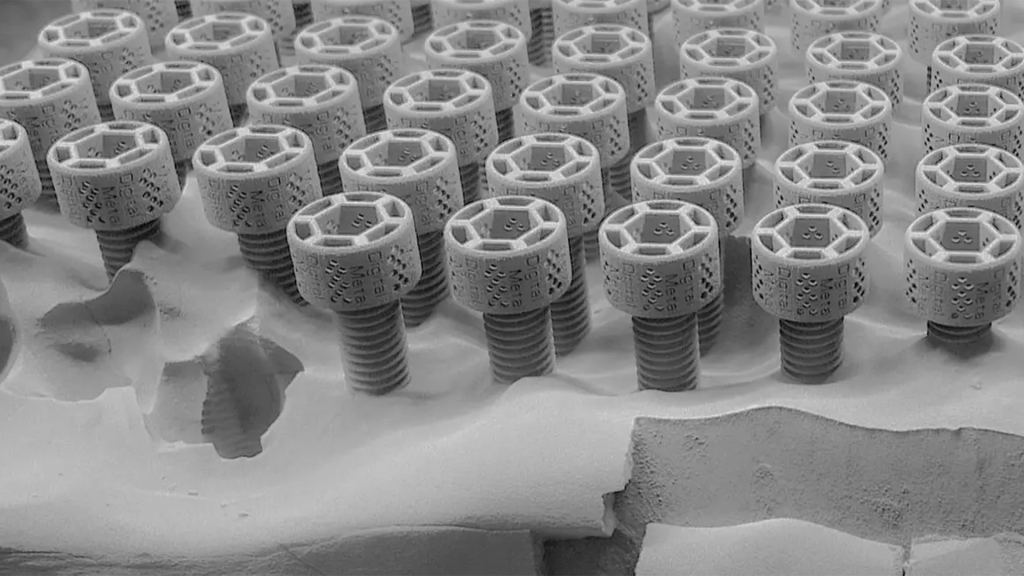 |
Технология металлической 3D-печати струйного нанесения связующего (MBJ) переживает ренессанс. За последнее десятилетие многие новые компании начали конкурировать друг с другом имея свой взгляд на использование этой технологии в промышленных 3D-принтерах.
Интерес к данной технологии подпитывается коммерческими возможностями, которые предоставляет технология металлической 3D-печати струйного нанесения связующего (MBJ). В первую очередь технология привлекает высокой скоростью 3D-печати и точностью производимых деталей. Процесс металлической 3D-печати технологии струйного нанесения связующего (MBJ) претендует стать новым методом крупносерийного производства. |
Но какие разработки способствуют развитию этой технологии?
В этой статье мы рассмотрим, как развивалась металлическая 3D-печать технологии струйного нанесения связующего (MBJ) и почему она становится новой технологией производства.
Истоки технологии металлической 3D-печати струйного нанесения связующего (MBJ)
|
Истоки технологии металлической 3D-печати струйного нанесения связующего (MBJ) начинаются в 1993 году, когда Массачусетский технологический институт (MIT) разработал процесс струйного нанесения металлических порошков для создания трехмерных объектов.
Интересно, что термин «3D-печать» был первоначально придуман Массачусетским технологическим институтом (MIT) в отношении технологии металлической 3D-печати струйного нанесения связующего (MBJ).
Производственная компания Extrude Hone Corporation получила эксклюзивную лицензию на технологию Массачусетского технологического института (MIT) в 1996 году. С тех пор компания разработала и коммерциализировала технологию металлической 3D-печати струйного нанесения связующего (MBJ), а первый 3D-принтер ProMetal RTS-300 был поставлен в компанию Motorola в 1999 году.
Компания ExOne отделившись от Extrude Hone Corporation в 2005 году, до начала 2010-х годов оставалась единственной компанией, которая использовала технологию металлической 3D-печати струйного нанесения связующего (MBJ). В то время срок действия ранних патентов Массачусетского технологического института (MIT) на технологию начал истекать, что позволило новым компаниям выйти на рынок со своими индивидуальными проектами. |
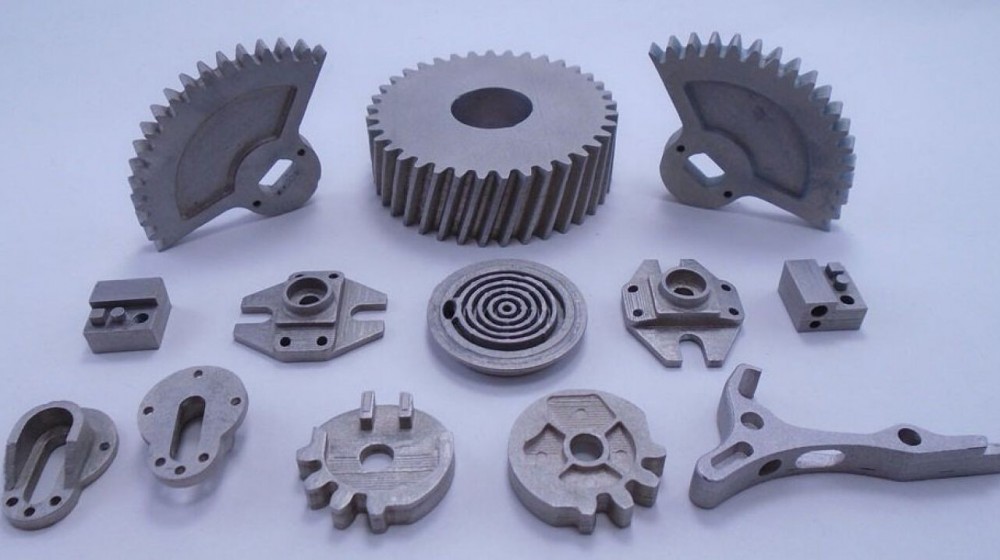 |
Суть технологии металлической 3D-печати струйного нанесения связующего (MBJ)
При металлической 3D-печати технологией струйного нанесения связующего (MBJ) жидкое связующее выборочно подается в порошковый слой для соединения частиц порошка, слой за слоем.
Процесс начинается с нанесения тонкого слоя порошка, при этом печатающие головки осаждают капли связующего вещества в порошковом слое. Затем платформа построения опускается и наносится следующий слой порошка.
Процесс повторяется до тех пор, пока изделие не будет построено на платформе построения, а неиспользованный порошок (около 95%) переработан для повторного использования.
При металлической 3D-печати технологией струйного нанесения связующего (MBJ) детали 3D-печати остаются хрупкими зеленными заготовками и требуют в дальнейшем процессы постобработки, такие как спекание и инфильтрацию для укрепления детали.
Помимо металлической 3D-печати технология струйного нанесения связующего может применятся в песчаных 3D-принтерах или пластиковых ПММА 3D-принтерах.
Этапы постобработки металлической 3D-печати технологией струйного нанесения связующего (MBJ)
|
Традиционно технология струйного нанесения связующего использует печатающую головку для нанесения жидкого связующего на слои порошка.
Также при металлической 3D-печати технологией струйного нанесения связующего (MBJ), детали 3D-печати требуют различные этапы постобработки, поскольку изначально они представляют собой зеленные заготовки, что означает, что они обладают низкими механическими свойствами и очень часто являются хрупкими. Этапы последующей обработки направлены на укрепление деталей и включают в себя: отверждение, спекание, инфильтрацию и другие процессы постобработки. |
Отверждение
Отверждение повышает прочность зеленых заготовок, поэтому их можно безопасно снять с платформы построения. Во время процесса изделия затвердевают в печи при температуре 200 С в течении нескольких часов, в результате чего изделия становятся намного прочнее. |
Спекание
Несмотря на отверждение, металлические изделия остаются по-прежнему очень пористыми. Однако можно значительно уменьшить пористость изделия за счет процессов спекания или инфильтрации. Обычно процесс спекания происходит в печи с контролируемой атмосферой, где изделие подвергается термообработке при температуре примерно 100 С в течении 24-36 часов, при этом связующее вещество выпаривается. Это приводит к сплавлению металлических частиц вместе и приводит к получению прочной металлической детали с низкой пористостью. Однако спекание может привести к неоднородной усадке детали, которую трудно предсказать, поэтому это необходимо учитывать на этапе проектирования. |
Инфильтрация
Для получения высокой плотности в изделии, ее необходимо инфильтрировать, чтобы заполнить пустоты, оставленные при выпаривании связующего вещества. Обычно это делается путем нанесения расплавленной бронзы для проникновения в оставшиеся пустоты в изделии. Прохождение этих этапов последующей обработки значительно улучшит механические свойства металлического изделия. Например, бронзовая инфильтрация нержавеющей стали может достичь конечной плотности 95%. |
Финишная обработка
Наконец, как вариант, деталь может быть отполирована и покрыта золотом или никелем, что позволяет получить эстетически привлекательную отделку поверхности. |
Почему 3D-печать металлического струйного нанесение связующего становится все более популярной технологией для производства?
Технология металлического струйного нанесения связующего обладает рядом уникальных преимуществ, облегчающих ее внедрение в производство. Давайте рассмотрим почему же эта технология так привлекательна для современного производства.
Во-первых, струйное нанесение связующего не расплавляет металлический порошок в процессе 3D-печати, что исключает проблемы, связанные с накоплением остаточных напряжений.
Во-вторых, технология металлического струйного нанесения связующего не требует никаких поддержек, поскольку во время 3D-печати детали окружены рыхлым, неиспользованным порошком. Оба эти преимущества позволяют свести к минимуму постобработку.
Кроме того, 3D-принтеры струйного нанесения связующего являются менее дорогостоящими, чем 3D-принтеры технологий селективного лазерного плавления (SLM) или прямой подвод энергии и материала (DED). Это объясняется тем, что в них не используются дорогостоящие лазерные установки или электронные пушки.
Разработанные новые 3D-принтеры технологии металлического струйного нанесения связующего могут также использовать порошки для литья металлов под давлением (MIM). Они значительно дешевле металлических порошков, чем разработанные специально для 3D-печати, которые обычно производятся в небольших объемах с использованием таких дорогостоящих методов производства, как газовая атомизация.
Помимо использование более дешевых порошков, технология струйного нанесения связующего производит 3D-печать деталей с высокой детализацией и с механическими свойствами, сравнимыми с теми, которые характерны для традиционного производства металлических изделий.
Наконец, скорость 3D-печати технологией металлического струйного нанесения связующего обычно выше, чем у других технологий 3D-печати металлических порошков. Все эти преимущества в совокупности позволяют масштабировать данную технологию для использования в серийном производстве.